Which factors should be considered when brass hot forging?
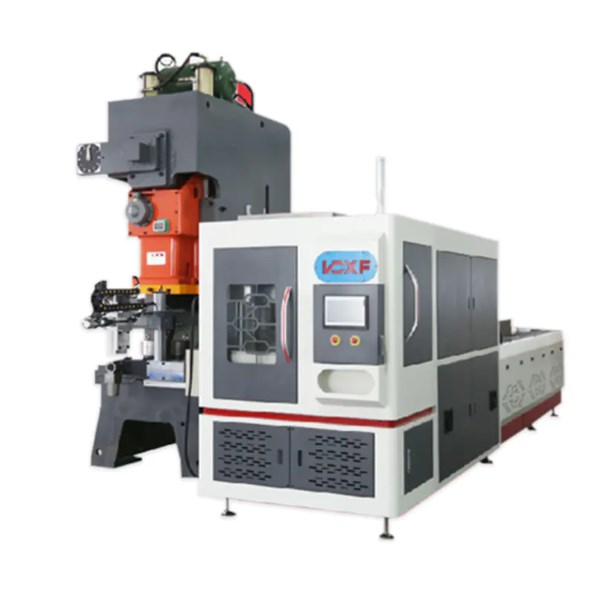
Brass hot forging is a process in which brass materials are shaped into the desired shape by external forces at high temperatures. Temperature, pressure and time are three crucial parameters, which together determine the quality and performance of brass hot forging products.
Temperature
Temperature is one of the most basic and critical factors in the process of hot forging. Brass hot forging usually needs to be carried out at higher temperatures, because brass alloys become softer and easier to shape at higher temperatures. However, the choice of temperature is not the higher the better, but to be precisely controlled according to the specific composition of the brass and the desired final product characteristics. Too high a temperature will cause the brass to oxidize and even melt, while insufficient temperature will make the material too hard to form, while increasing the risk of mold wear. Therefore, finding the right heating temperature to make the brass achieve the best plastic state is the first step in the successful brass hot forging.
Stress
Pressure is a direct means of shaping brass into a particular shape. During the hot forging process of brass, pressure is applied to the heated brass through the die, causing it to flow and fill every detail of the die. The size of the pressure directly affects the accuracy and surface quality of the product. If the pressure is insufficient, the brass may not be able to fill the mold completely, resulting in problems with cavities or insufficiently formed products; excessive pressure may lead to excessive material flow, affecting the dimensional stability of the product. Therefore, precisely controlling the pressure to ensure that the brass can flow evenly in the die is another key point in the hot forging process.
Time
Time is an often overlooked factor in the brass hot forging process, but it is just as important. In brass hot forging, the heating time, holding time and cooling time all have significant effects on the final product quality. Proper heating time can ensure uniform material temperature and avoid internal stress; the holding time is to make the material reach and maintain the optimal hot forging temperature; the cooling rate affects the microstructure of the material, which in turn affects the mechanical properties of the product. Rapid cooling may cause cracks inside the material, while slow cooling may reduce the hardness of the material. Therefore, a reasonable arrangement of the time of each stage is crucial to ensure the comprehensive performance of hot forgings.
- Art
- Causes
- Crafts
- Crypto
- Dance
- Drinks
- Defi
- Film
- Fitness
- Food
- Giochi
- Gardening
- Health
- Home
- Literature
- Music
- Networking
- Altre informazioni
- Party
- Religion
- Shopping
- Sports
- Theater
- Wellness