Overcoming Dust Challenges to Keep Custom Mobile Impact Crushers Running Smoothly
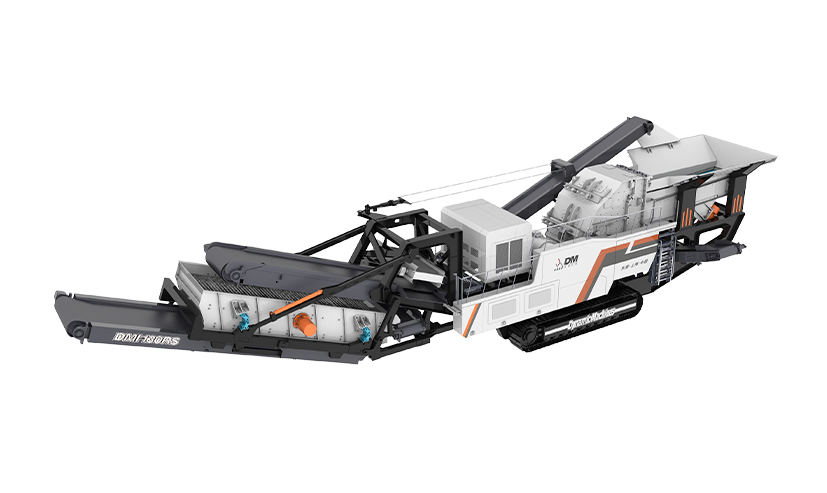
Custom Mobile Impact Crushers (CMICS) are indispensable in the mining and quarrying industries for their ability to crush rocks and other materials into smaller sizes. However, these crushers often operate in environments with high levels of dust, which can pose significant challenges to their performance and longevity. Addressing these challenges requires a comprehensive approach that encompasses design considerations, operational protocols, and maintenance routines.
Design Considerations for Dust Mitigation
The design of a CMICS must account for the harsh realities of high-dust environments. This includes incorporating dust suppression systems, such as misting or water sprays, which help to reduce the amount of airborne particles. The enclosure of critical components, such as engines and electrical systems, is also crucial to prevent dust ingress that can lead to overheating and electrical shorts.
Operational Protocols for Dust Management
Operational protocols play a significant role in managing dust around CMICS. This includes regular cleaning schedules to remove accumulated dust from the crusher's exterior and interior components. The use of dust barriers or windbreaks can also be employed to reduce the direct impact of dust on the crusher during operation.
Maintenance Routines to Combat Dust
A robust maintenance routine is essential for CMICS operating in high-dust conditions. Regular inspections and servicing ensure that dust does not compromise the integrity of the crusher's components. This includes cleaning or replacing air filters, lubricating moving parts to prevent dust adhesion, and checking for any signs of wear or damage that could be exacerbated by dust.
Use of Advanced Filtration Systems
Advanced filtration systems can be integrated into CMICS to further protect internal components from dust. High-efficiency particulate air (HEPA) filters can be used to trap fine dust particles before they reach sensitive areas, such as the engine and hydraulic systems.
Automation and Sensor Technology
The incorporation of automation and sensor technology can help to monitor dust levels around the CMICS and adjust operations accordingly. Sensors can trigger dust suppression systems when dust levels exceed safe thresholds, and automated systems can adjust crusher settings to minimize dust generation during the crushing process.
Protective Coatings and Materials
Using protective coatings and materials that are resistant to dust abrasion can prolong the life of CMICS. Coating critical parts with dust-resistant materials can reduce wear and tear, while choosing materials that are less prone to dust adhesion can make cleaning more effective.
Training and Awareness
Finally, training operators and maintenance staff on the specific challenges of high-dust environments is crucial. Awareness of the importance of dust management and the steps to take to mitigate its effects can significantly improve the performance and longevity of CMICS.
In conclusion, ensuring the normal operation of Custom Mobile Impact Crushers in high-dust environments requires a multifaceted approach that includes design enhancements, operational protocols, regular maintenance, the use of advanced technologies, and proper training. By addressing these aspects, the performance and service life of CMICS can be significantly improved, even in the most challenging conditions.
Mobile Impact Crusher Feed Particle Size: ≤650mm
Processing Capacity: 80-360t/h
Machinery Weight: 45-62t
- Art
- Causes
- Crafts
- Crypto
- Dance
- Drinks
- Defi
- Film
- Fitness
- Food
- Games
- Gardening
- Health
- Home
- Literature
- Music
- Networking
- Other
- Party
- Religion
- Shopping
- Sports
- Theater
- Wellness