How Carbide Rotary Burs Provide Cutting Benefits Compared to Conventional Tools
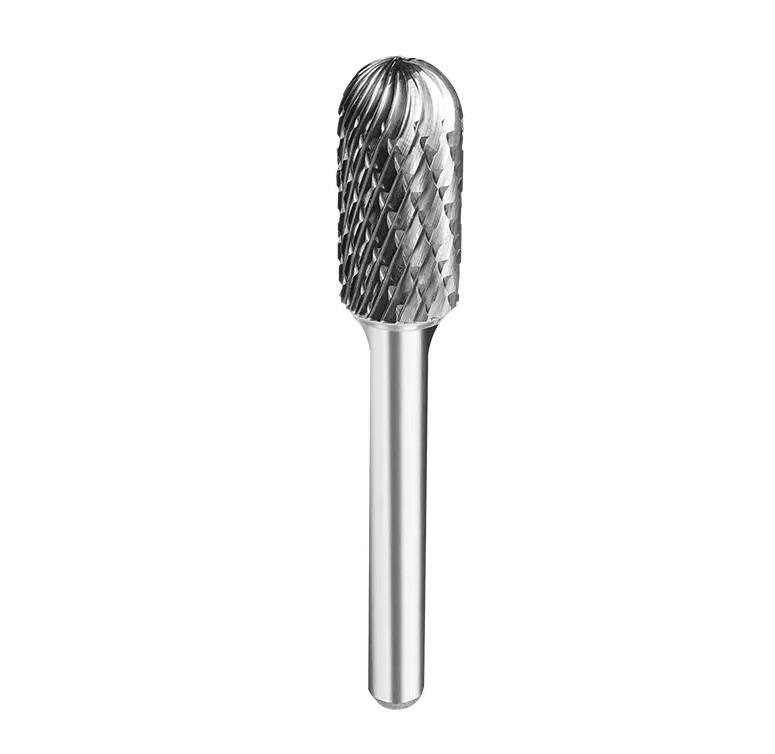
In the world of metal fabrication and precision machining, choosing the right tool can significantly impact efficiency, surface quality, and overall productivity. Among the many tools available for material removal and surface shaping, Carbide Rotary Burs have emerged as a standout choice due to their remarkable combination of hardness, versatility, and cutting performance. When compared to other traditional metalworking tools, such as high-speed steel (HSS) cutters, grinding wheels, and sanding abrasives, Carbide Rotary Burs offer several distinct advantages that make them indispensable in both industrial and artisanal settings.
One of the primary advantages of Carbide Rotary Burs is their exceptional durability. Made from tungsten carbide, one of the hardest materials available for tooling, these burs can maintain their sharpness and cutting integrity far longer than conventional tools made of HSS or coated steels. This translates into significantly less downtime for tool changes and lower long-term tooling costs. In environments where continuous, high-volume machining is required, this durability leads to increased uptime and enhanced productivity.
Another critical benefit is the precision that Carbide Rotary Burs provide. Unlike grinding wheels or flap discs, which can be bulky or imprecise in tight or intricate spaces, rotary burs are available in a wide variety of shapes and sizes. This allows machinists to perform detailed contouring, engraving, and edge blending with a high degree of control. Whether working on complex molds, fine weld seams, or internal surfaces, carbide burs can reach areas that other tools simply cannot, all while delivering a smooth and consistent finish.
Versatility is also a key factor in the superiority of Carbide Rotary Burs. They are capable of cutting through a broad range of materials, including hardened steels, stainless steel, cast iron, aluminum, brass, titanium, and even non-metals like fiberglass and plastics. This makes them highly adaptable tools for multi-material environments such as aerospace, automotive, and medical device manufacturing. Traditional tools like files, saw blades, or abrasives may be limited in the types of materials they can handle or may require frequent switching to suit different tasks. Carbide rotary burs streamline these operations, reducing the need for multiple tools.
Heat resistance is another area where carbide burs shine. Unlike tools that deform or dull quickly under high temperatures, Carbide Rotary Burs maintain their performance even in dry cutting conditions or when used on materials that generate significant friction. This is especially valuable in production scenarios where coolant is minimal or absent. Their ability to withstand high operational heat without losing structural integrity not only preserves the tool itself but also protects the workpiece from thermal damage.
Furthermore, the cutting efficiency of Carbide Rotary Burs is notably higher than many alternatives. Their sharp, precision-ground flutes allow for aggressive material removal while still producing fine finishes, effectively combining the functions of roughing and finishing tools in a single pass. This dual functionality helps reduce cycle times and increases workflow efficiency, an essential factor in competitive manufacturing environments.
In conclusion, while many tools are available for metalworking tasks, Carbide Rotary Burs consistently outperform others in durability, precision, versatility, heat resistance, and cutting speed. Their ability to streamline complex operations, extend tool life, and deliver high-quality results across a wide array of materials makes them a superior choice for modern machinists. As technology advances and demands for accuracy and efficiency increase, Carbide Rotary Burs continue to prove themselves as a cornerstone of advanced metalworking solutions.
Cut type: Particularly suitable for working on aluminum, magnesium, plastic, and hard rubber. Gives high cutter efficiency, with good removal of material. The specific features of this type of cut facilitate rapid removal of chips, preventing these from clogging the tool.
- Art
- Causes
- Crafts
- Crypto
- Dance
- Drinks
- Defi
- Film
- Fitness
- Food
- Jogos
- Gardening
- Health
- Início
- Literature
- Music
- Networking
- Outro
- Party
- Religion
- Shopping
- Sports
- Theater
- Wellness