The Importance of Balanced Clamping Pressure When Using Round Drain Baskets Moulds in Production
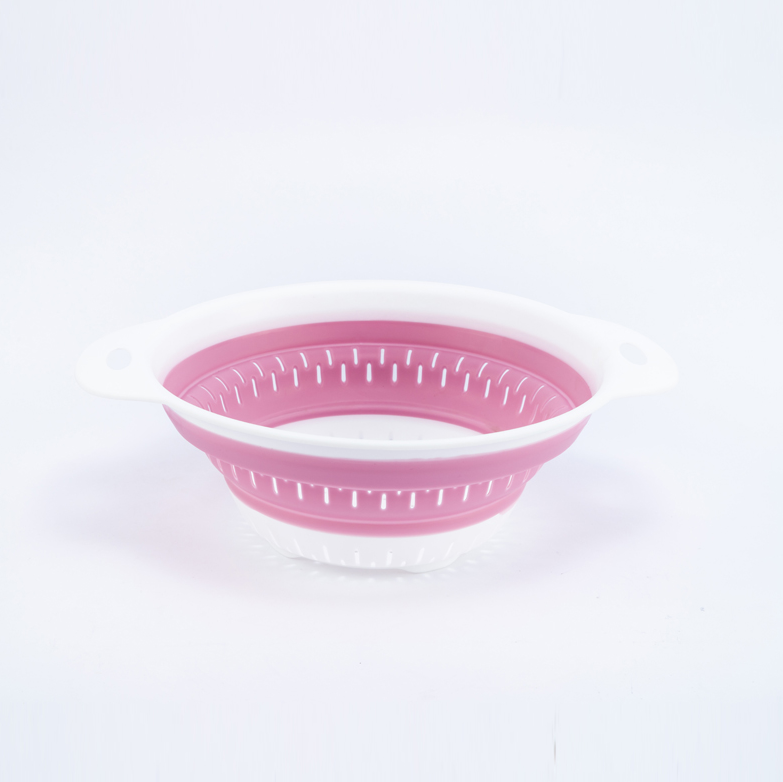
Controlling the clamping force during the production of parts using Round Drain Baskets Moulds is essential for ensuring product quality, minimizing defects, and protecting mould integrity. Clamping force refers to the pressure applied by the injection moulding machine to keep the two halves of the mould closed during the injection and cooling phases. If the force is insufficient, the mould may separate slightly, allowing molten plastic to escape and form unwanted flash around the part. Conversely, excessive force can lead to unnecessary wear on the machine and mould, reduced cycle efficiency, and even deformation of delicate mould features, especially in high-cavity or thin-walled applications such as drain baskets.
To achieve optimal clamping force, manufacturers begin by calculating the projected area of the part, which is the surface area of the mould cavity that is perpendicular to the direction of injection. This area, combined with the injection pressure of the selected resin, determines the minimum clamping force required to keep the mould securely closed. For Round Drain Baskets Moulds, which often involve thin walls and multiple drain holes, this calculation must be especially precise, as variations in wall thickness or mould complexity can significantly influence how force is distributed during injection.
Proper alignment of the mould within the injection machine is also a critical factor. If the mould is not evenly seated or if the platens are not parallel, uneven clamping force may result, leading to localized flashing or damage. High-precision mould bases and robust alignment systems help maintain the uniform pressure necessary for consistent part quality. In some cases, specially designed support pillars or additional locking mechanisms are used to enhance mould stability during high-pressure injection cycles.
Another key consideration is the behavior of the resin material during the moulding cycle. Different thermoplastics exert varying cavity pressures depending on their viscosity, flow characteristics, and shrinkage rates. For example, high-flow resins may require lower injection pressures, which in turn reduce the clamping force needed. However, materials prone to shrinkage or warping might place uneven stress on the mould, especially if cooling is not uniform. Therefore, real-time process monitoring is often employed to adjust clamping force dynamically based on cycle feedback, ensuring optimal sealing throughout each injection shot.
Modern injection moulding machines offer servo-hydraulic or electric clamp systems that allow precise control and repeatability of clamping force settings. This level of control is especially valuable for Round Drain Baskets Moulds, where consistent dimensional accuracy and hole alignment are critical to product function. These machines often include sensors that monitor mould deflection, platen movement, and internal cavity pressure, allowing for automatic adjustments during production. This technology helps prevent overclamping, which could cause fatigue in the mould or misalignment in mould components over time.
Additionally, the use of mould protection features, such as low-pressure closing and touch-sensitive clamping, can prevent damage when foreign material is present or when mould misalignment occurs. This protective approach further ensures the longevity of the mould and reduces the likelihood of costly downtime or part rejection.
In conclusion, controlling the clamping force during the operation of Round Drain Baskets Moulds involves a careful balance of engineering calculations, machine capability, material properties, and process monitoring. Proper clamping not only ensures the part is formed accurately and consistently but also extends the service life of the mould and the efficiency of the entire production line. Through advanced equipment and process optimization, manufacturers can maintain ideal moulding conditions that result in high-quality, uniform products with minimal waste and maximum reliability.
Name: Round Drain Basket
Mould material: S136
Mould base: P20 steel
Cavity NO: 1+1
Product material: PP+TPR
Runner: Hot/cold
Mould life: 1 million~3 million shots
Delivery time: 35~50 days
- Art
- Causes
- Crafts
- Crypto
- Dance
- Drinks
- Defi
- Film
- Fitness
- Food
- Jogos
- Gardening
- Health
- Início
- Literature
- Music
- Networking
- Outro
- Party
- Religion
- Shopping
- Sports
- Theater
- Wellness