Automotive Interior Injection Plastic Part Molding: Precision Engineering for Modern Vehicles
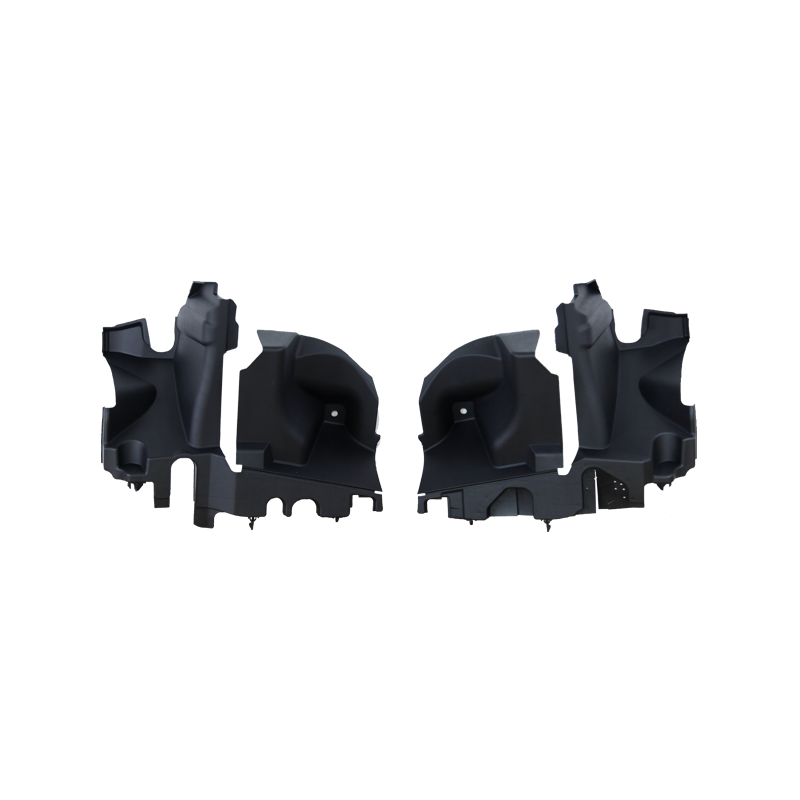
Automotive Interior Injection Plastic Part Molding is a cutting-edge manufacturing process tailored to produce high-performance, durable, and lightweight components for vehicle interiors. By utilizing advanced engineering plastics such as ABS, PC, and PP, this technology enables the creation of intricate parts that meet stringent automotive standards while optimizing weight reduction.
The core advantage of Automotive Interior Injection Plastic Part Molding lies in its ability to deliver lightweight solutions without compromising structural integrity. Components like dashboard panels, trim pieces, air vents, and control knobs manufactured through this method contribute to overall vehicle weight reduction. This directly enhances fuel efficiency in combustion engines and extends the driving range of electric vehicles, aligning with global sustainability goals.
Heat resistance and flame retardancy are critical in automotive interiors, and Automotive Interior Injection Plastic Part Molding excels in both. Materials such as ABS and PC withstand high temperatures encountered in cabin environments, while meeting rigorous flame retardancy standards like UL 94 V-0. This ensures passenger safety and compliance with automotive industry regulations.
The flexibility of Automotive Interior Injection Plastic Part Molding allows for complex geometries and high-precision designs, enabling seamless integration of functional features like snap-fit assemblies, textured surfaces, and integrated mounting points. This versatility supports innovation in interior aesthetics and ergonomics, catering to evolving consumer preferences.
Moreover, the process emphasizes cost-efficiency and scalability. High-volume production runs maintain consistent quality, while recyclable plastics align with circular economy principles. Manufacturers leveraging Automotive Interior Injection Plastic Part Molding benefit from reduced material waste, faster cycle times, and enhanced durability of end products.
In summary, Automotive Interior Injection Plastic Part Molding is the cornerstone of modern automotive interior design, combining lightweight engineering, superior thermal performance, and flame safety. As the automotive industry shifts toward electrification and sustainability, this technology remains pivotal in shaping safer, lighter, and more efficient vehicles for the future.
- Art
- Causes
- Crafts
- Crypto
- Dance
- Drinks
- Defi
- Film
- Fitness
- Food
- Jogos
- Gardening
- Health
- Início
- Literature
- Music
- Networking
- Outro
- Party
- Religion
- Shopping
- Sports
- Theater
- Wellness