Why Safety and Consistency Are Core Values in Every Pressure Control Factory Operation
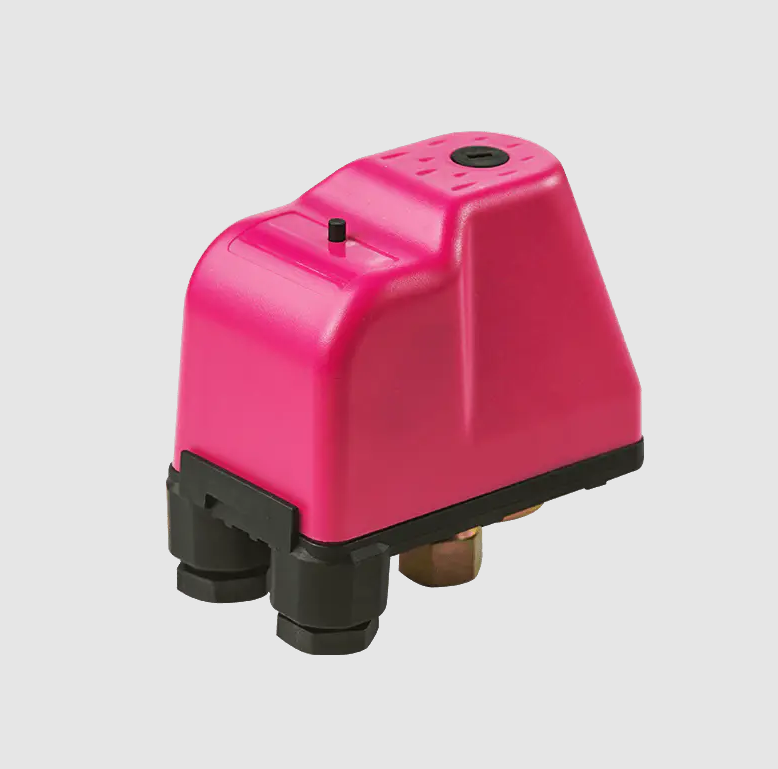
In industries that depend on reliable fluid and gas management, such as energy, pharmaceuticals, chemical processing, and aerospace, the safety and consistency of pressure control equipment are non-negotiable. Failures can lead to hazardous conditions, costly downtime, or even catastrophic damage. This is why a reputable Pressure Control Factory must prioritize both safety and consistency throughout its production process. Ensuring these two critical factors is not the result of a single step, but rather the culmination of comprehensive design principles, rigorous quality control, advanced manufacturing practices, and stringent testing protocols—all working in harmony.
A professional Pressure Control Factory begins by embedding safety into its product design philosophy. Before any physical component is produced, engineers use simulation software and stress analysis tools to evaluate structural integrity under a variety of conditions, ranging from overpressure and thermal expansion to corrosive exposure and fatigue cycles. These pre-manufacturing evaluations allow the factory to identify potential failure points and implement safety redundancies, such as pressure relief mechanisms or fail-safe valves. It ensures that every product has a built-in margin for safety, even when operating under extreme conditions.
Once the design is finalized, the Pressure Control Factory ensures consistency through highly controlled manufacturing environments. Advanced CNC machining and robotic assembly lines are employed to fabricate components to exacting tolerances. These automated systems drastically reduce human error and guarantee that each unit conforms to the original specifications. Critical components such as valve bodies, diaphragms, and sealing surfaces are measured with sub-millimeter precision using laser and vision inspection systems. The uniformity in production not only contributes to consistency but also plays a vital role in achieving long-term safety, as even the smallest deviation can affect sealing performance or cause structural fatigue over time.
Material traceability is another key element that underpins both safety and consistency in a Pressure Control Factory. Every component can be traced back to its material source, batch number, and supplier certification. This is crucial in ensuring that all materials used—especially in high-pressure or chemically aggressive applications—meet global standards for strength, corrosion resistance, and thermal performance. Without traceability, even the most well-designed system is at risk due to material variability.
Throughout the production process, the Pressure Control Factory employs robust quality assurance protocols, including multiple inspection stages. Initial inspections check raw material conformity; in-process inspections validate machining accuracy; and final inspections include hydrostatic testing, leak testing, and sometimes even destructive testing of sample units. Many factories adhere to internationally recognized quality systems such as ISO 9001, ASME, or CE, which require thorough documentation, repeatability in results, and continuous process improvement.
To enhance safety further, a Pressure Control Factory may also perform lifecycle testing on pressure control products, simulating years of operation within a matter of days or weeks. These tests expose products to rapid pressure cycling, temperature swings, and vibration to identify any long-term weaknesses. Only units that pass these extreme tests are approved for delivery, especially in mission-critical industries like aerospace or nuclear energy.
Finally, the commitment to safety and consistency doesn’t end once the product leaves the factory. A top-tier Pressure Control Factory offers full technical documentation, user training, installation guidelines, and post-sale support. These services ensure that customers operate the equipment correctly, preserving the safety and performance standards built into every unit.
The device's working principle involves dual control of Pressure and flow. The water pump turns on and off automatically when the water pressure changes based on water consumption.
- Art
- Causes
- Crafts
- Crypto
- Dance
- Drinks
- Defi
- Film
- Fitness
- Food
- Jogos
- Gardening
- Health
- Início
- Literature
- Music
- Networking
- Outro
- Party
- Religion
- Shopping
- Sports
- Theater
- Wellness